研究背景
机床铸件是机械制造中常见的零部件,其质量和性能直接影响着整机的使用效果。在机床铸件的生产过程中,时效处理是一种常见的工艺方法,通过控制材料的组织结构和性能来提高铸件的强度和耐磨性。时效处理的参数选择和优化一直是一个复杂而困难的问题,需要综合考虑材料的成分、热处理工艺和设备条件等多方面因素。
研究意义
机床铸件的时效处理对提高零部件的使用寿命、降低能耗和提高生产效率都具有重要意义。对机床铸件时效处理的优化研究不仅可以提高零部件的质量和性能,还可以为机械制造行业的发展提供技术支持和指导。
研究方法
本研究将采用实验方法和数值模拟相结合的方式进行。通过对不同工艺参数下的机床铸件进行时效处理,并对其性能进行测试和分析,得到不同工艺参数下的性能数据。然后,利用数值模拟方法,建立机床铸件的热处理过程模型,通过模拟分析不同参数对材料组织和性能的影响,进一步优化时效处理的工艺参数。
研究内容
1. 机床铸件的材料选择和成分设计
2. 时效处理工艺参数的选择和优化
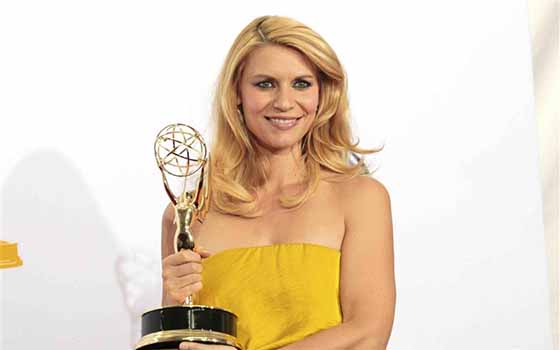
3. 时效处理对机床铸件性能的影响分析
4. 时效处理过程的数值模拟建模
5. 时效处理工艺参数的优化方法研究
6. 优化后机床铸件的性能测试和分析
研究成果
通过对机床铸件时效处理工艺的优化研究,可以得到不同工艺参数下的最佳时效处理方案,进一步提高机床铸件的强度、硬度和耐磨性等性能指标。通过数值模拟方法,可以深入了解时效处理过程中材料组织和性能的变化规律,为工艺参数的选择和优化提供科学依据。
研究展望
本研究还可以进一步拓展到其他材料和工艺的研究领域,如铝合金、镁合金等材料的时效处理优化研究,以及其他热处理工艺的优化研究。还可以结合智能制造和大数据分析等新技术手段,进一步提高机床铸件时效处理工艺的精度和效率。